昔の金属AM
金属のアディティブ・マニュファクチャリング(AM)がますます身近な存在となってきましたが、実は金属の積層造形装置は過去にも注目を浴びたことがあります。1996年頃、弊社が金属粉末の積層造形装置 EOSINT M250の販売を開始して間もなくのころですね。当時は携帯電話を筆頭に、家電、自動車向けなどで金型業界が隆盛を極めていた時期で、金型業界あるいは大企業の金型製作部門の新しい生産設備・生産技術に対する投資意欲はとても大きなものであったと記憶しています。
そんな中、金属の積層造形装置で金型を早く、安くつくれるのではないか?ということで実際に装置を導入した企業は少なくありません。当然、当時のレーザエネルギー、金属材料では造形物の強度や密度が十分ではなかったのですが、それでも我々もお客様と一緒になって何とか使い物になる金型ができないものかと試行錯誤をしたものです。
中には積層造形のメリットを活かせたお客様も居られましたが、大方の評価は強度(密度)、精度、コスト、品質すべての点で機械加工には勝てないなあというものでした。結果として「金属造形はまだまだだなあ」という認識を世の中に広めてしまったのは残念なことです。
当時の評価項目がコスト、時間(工数)が主であったということも一因だと思います。造形物をミリングで追加工するようなことも受け入れられなかったですし。
現在の金属AM
現在、AMは従来工法では不可能であった高機能部品がつくれる、ということで注目を集めています。
具体的にはラティス構造やトポロジー最適化による軽量・高強度の部品、コンフォーマル冷却水路を張り巡らせた金型、複雑構造の一体化造形、高効率熱交換器などです。これも高いエネルギー密度を発生できるレーザ、高強度、高耐熱性の材料が使えるようになった恩恵ですが、話はそんなに簡単なものではありません。
金属粉末をピンポイントで溶融して急冷して固める。それを順次繋げていって線にし、更にその線を横に広げて面にする。さらに面を積み重ねて立体にする。
基本的に局所的な加熱による応力の発生(=変形)が避けられない工法なので、ごく単純な立体形状でも精度良く、均一で高い密度で、そこそこの表面品質で造形することは簡単なことではありません。 ましてそんな素性の工法でラティス構造だのトポロジー最適化形状だの複雑構造の一体化造形だのと、簡単に造形できることではないことは容易に想像がつきます。
また造形物の評価はどうするのか?ということも重要な問題となります。
結局、「使い物になる部品をつくるということに関しては今も昔も膨大な試行錯誤が必要で有る」という結論になると思います。 但し、今と昔では大きな違いがあります。
それは、今我々が手にしているのは、頑張ればその苦労が報われる装置になっているということです。
この装置を買いさえすれば誰もが高機能部品をつくれるのか?と問われれば、答えはNoです。今のところ、そこまで完成された機械ではありません。しかし、頑張った人には微笑んでくれる、そんな人間らしい機械が私は好きです。
著者紹介
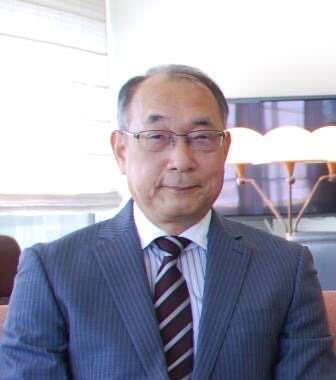
略歴
1952年 大阪生まれ
1977年 大阪府立大学大学院工学研究科船舶工学 修士課程修了
1978年 日立造船情報システム(株)入社
1991年 海外事業部部長
1993年 独EOS社と積層造形装置の日本国内における独占販売契約締結。
以後、EOS社の積層造形装置の事業推進に従事し、現在に至る。
2021年 2月1日現在
(株)NTTデータ ザムテクノロジーズ ソリューション統括部 技術部