金属積層造形装置の起源
金属粉末を積層的に固めて3次元の金属部品を造形する装置は、1992年にDTM社(後に3D Systems社が買収)が製品化したSinterstationがその起源でしょう。テキサス大学で開発されたSelective Laser Sintering(SLS)、今でいうところのPowder Bed Fusionの技術を用いた装置です。但しこの装置は金属造形専用ということではなく、ポリマー材料用の造形装置をそのまま金属に適用したものであり、材料には金属粉末にレジンをコーティングしたものを使用していました。
造形物は「グリーンパーツ」と呼ばれ、非常に壊れやすく取扱には細心の注意が必要でした。グリーンパーツは炉で他の金属を溶侵させる2次工程が必要で、その際の精度の保持が難しいものでした。溶侵に必要な金属量を正確に投入する必要があったという話も聞いております。
1995年にはEOS社がEOSINT Mを発表し、金属をレーザで直接焼結するDirect Metal Laser Sintering(DMLS)方式を前面に打ち出し、DTM社との差別化を図りました。しかし、金属を完全に溶融するのではなく融点の低い金属で融点の高い金属を固着させるような形であり、強度や密度が実際の部品や量産用の金型に使えるものではありませんでした。
1997年にはArcamから真空チャンバと電子ビームを採用したEBM方式の装置が発表され、その後も複数のメーカからDirect Metal Deposition(DMD) 方式や粉末のレーザ焼結(溶融)と切削加工を組み合わせたHybrid方式などの装置が製品化されています。
初期の金属造形は造形物の強度、密度、精度、表面品質が製品として満足できるものではなく「金属造形はまだまだ使い物にならないな」というのが大方の評価だったと思います。いくら磨いても顔を出してくる空孔にはがっかりさせられたものです。
金属造形の進化
金属造形が部品や金型の製作ツールとして意識されるようになったのは、ファイバーレーザを搭載した装置が出現した2004年以降のことです。同じ200Wのレーザで比較しても、従来のCO2レーザのビーム径が0.3 – 0.5mmであるのに対して、ファイバーレーザのビーム径は0.1mmであり大きなエネルギー密度が投入できるようになりました。また、マレージング鋼の実用化により、強度があり密度が高く変形の少ない造形が可能になったことも、金属造形が日の目を見るようになった理由となります。
その後もチタン合金やニッケル基合金などの高機能材料が開発され、適用できる用途も大きく広がりました。実際、ジェットエンジンの燃料噴射装置など、3Dプリンタで量産される製品も現れてきています。
現在
気が付けば、3Dプリンティング無しでは、航空機の省燃費を達成できない! レースに勝てない! 予算内でロケットを打ち上げられない!
そんな世の中になってしまっています。
でも、3Dプリンティングでものをつくること、特に金属のアディティブ・マニュファクチャリング(AM)を実現することは簡単なことではありません。その辺の話はまた別の機会にお話ししたいと思います。
著者紹介
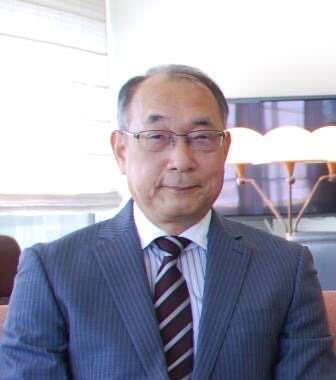
略歴
1952年 大阪生まれ
1977年 大阪府立大学大学院工学研究科船舶工学 修士課程修了
1978年 日立造船情報システム(株)入社
1991年 海外事業部部長
1993年 独EOS社と積層造形装置の日本国内における独占販売契約締結。
以後、EOS社の積層造形装置の事業推進に従事し、現在に至る。
2021年 2月1日現在
(株)NTTデータ ザムテクノロジーズ ソリューション統括部 技術部