3Dプリンタに思うこと
今日は少し趣向を変えて、3Dプリンタに関して常に心の片隅に常に引っかかっていることを白状したいと思います。
光造形にしてもレーザ焼結にしても、レーザビームをガルバノスキャナで所定の断面形状に照射するという原理は装置の出現以来、今日まで変わっていません。すなわちx軸用、y軸用の二面のミラーを物理的に駆動して造形面にある所定の断面を塗りつぶすという制御になるわけですね。
金属造形に使われているYbレーザの場合、レーザビーム径は約0.1mmです。
すなわち一本のレーザ軌跡が固める線の幅は熱の拡散も考慮してもせいぜい0.3mmといったところでしょうか。
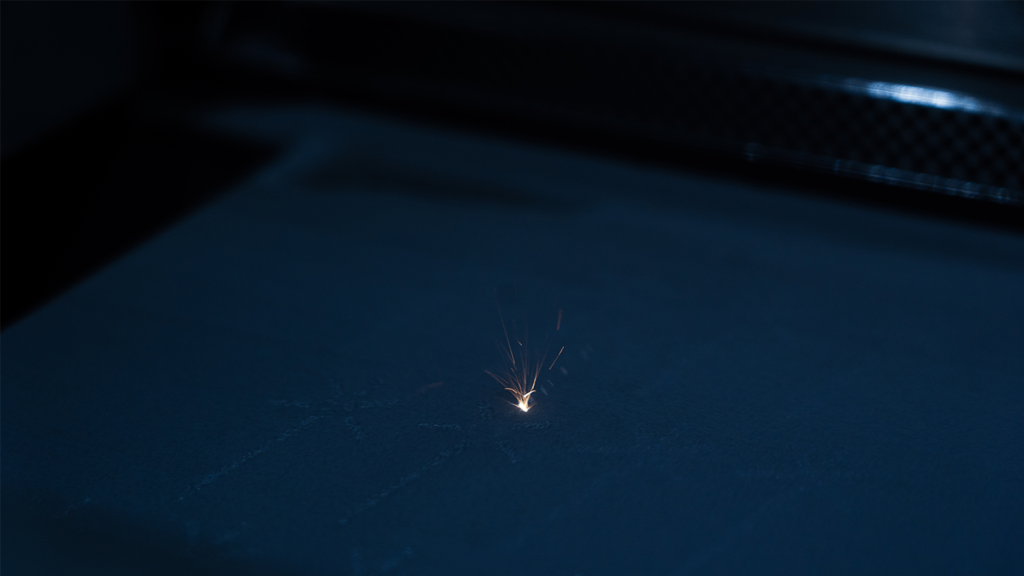
一方、造形領域の容積はEOS M 290 の場合で 250mm x 250mm x 325(造形プラットフォーム厚さ含む)mmあります。また1層の厚さは最小で0.02mm、積層高さが300mmだと15,000層もの数になります。
何が言いたいかというと、これって例えば0.3mmのシャーペンで15,000枚もの断面形状を塗りつぶしているのと同じ、なんかティースプーンで井戸を掘っているのと同じじゃないかなあという素朴な疑問が沸いてきます。
もう一つ思うこと
レーザビームの造形面での走査速度は最大で7m/s、造形面は広いところもあれば細いスリット状のところもありますが、ガルバノミラーの駆動周波数も大変な数字になります。大変荒っぽい計算をすると例えば7mm x 70mmの細長い領域を最大速度で走査すると短辺方向では500Hz、長手方向では50Hzになります。それが長いジョブだと1週間も動きっぱなしになるわけです。
定期的にキャリブレーションはするにしても、そんな過酷な使われ方をされても何年も故障もせずに精度をキープできるというのはすごい部品だなあと感心します。ガルバノミラーに限らずレーザや直動システムなど高性能な部品はどの3Dプリンタメーカーも採用しているでしょう。結局3Dプリンタの優劣を決めるのは造形プロセスを十分理解したうえでの装置構成、装置制御、造形パラメータなのかなあと思う次第です。
著者紹介
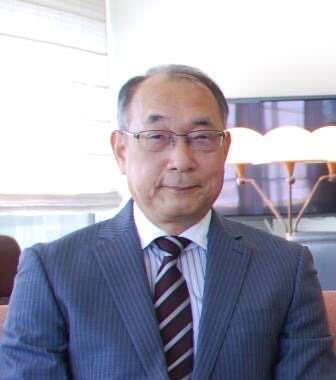
略歴
1952年 大阪生まれ
1977年 大阪府立大学大学院工学研究科船舶工学 修士課程修了
1978年 日立造船情報システム(株)入社
1991年 海外事業部部長
1993年 独EOS社と積層造形装置の日本国内における独占販売契約締結。
以後、EOS社の積層造形装置の事業推進に従事し、現在に至る。
2021年 2月1日現在
(株)NTTデータ ザムテクノロジーズ ソリューション統括部 技術部