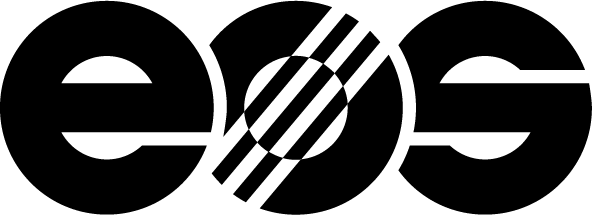
EOSは、金属3Dプリンターの造形プロセスの改善について積極的に取り組んでいます。
ここではEOSによるプロセスイノベーションと、部品単価を下げる方法についてご紹介します。
※本記事は、2024年2月2日に開催されたTCT Japan 2024 Introducing Stageでの講演をもとに構成しています。
目次
スパッタと欠陥
金属3Dプリンターでの製造過程では、レーザー溶接と同様に火花のようなスパッタの飛散が発生します。
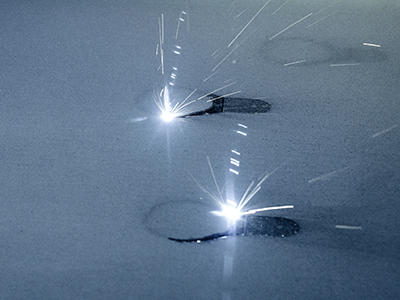
スパッタは溶融の挙動に影響を与えるため、EOSではスパッタの飛散を大幅に減少させる新しい照射プロセスを開発しています。
標準プロセスとの比較
スパッタの比較
通常は金属粉末の上からレーザーを照射しますが、よりスパッタが鮮明に見えるように、ここでは金属のプレート(ベースプレート)上に直接照射しています。
前半の照射が標準のプロセスで、後半が最適化後のプロセスです。
最適化後はスパッタの飛散がかなり少ないのが確認できます。
次は金属粉末(パウダーベッド)上からの照射での比較です。
こちらも、最適化後のプロセスではスパッタの飛散が少ないことが確認できます。
欠陥の比較
次は、プロセスによって内部欠陥に差があるかを比較します。
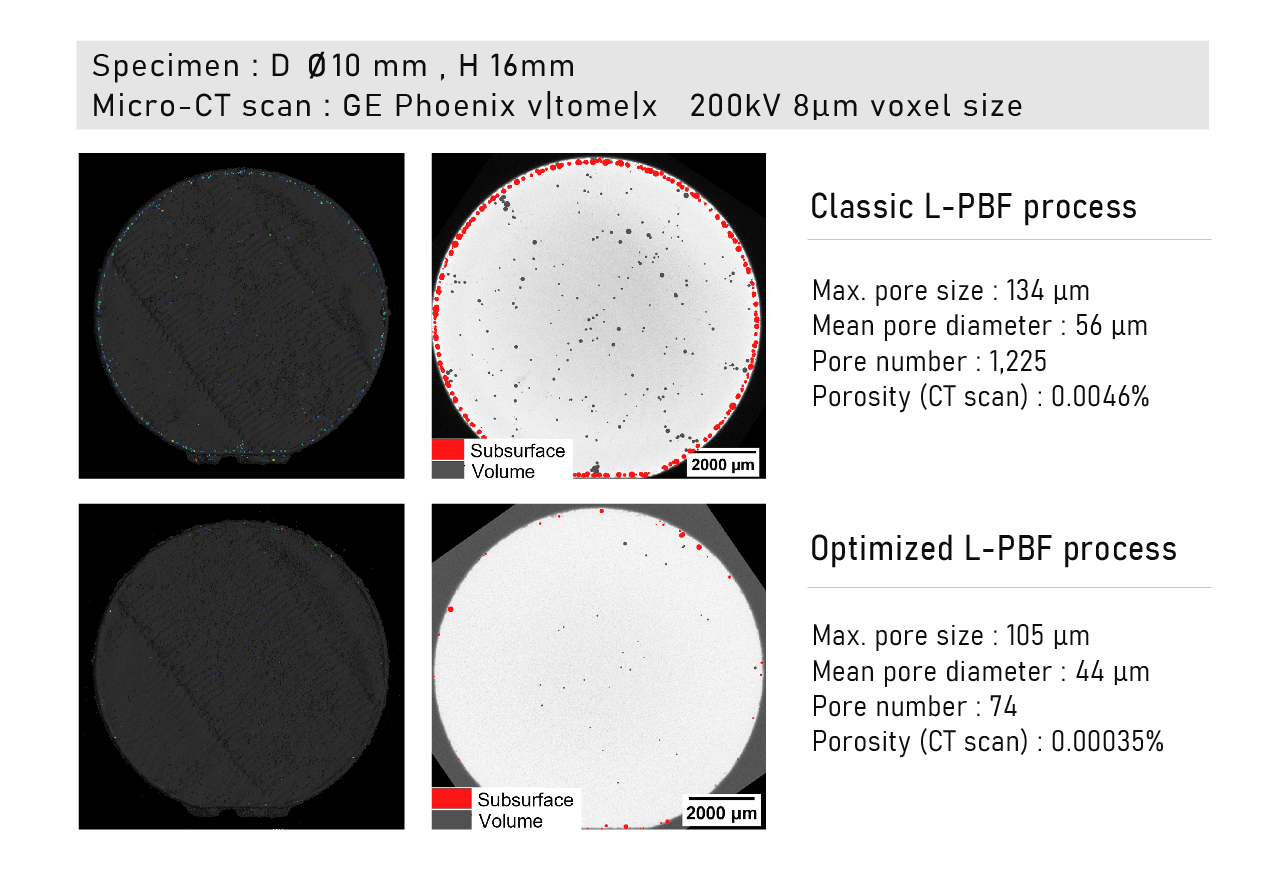
上が標準のプロセスで、下が最適化後のプロセスでの結果です。
標準のプロセスに比べ、最適化後のプロセスの方が欠陥が少ないことが確認できます。
欠陥の数や最大欠陥サイズへの効果が大きいと言えます。
高度なパラメータ開発
ダウンスキンパラメータ
EOSのSmart Fusionからヒントを得て開発した、ダウンスキンパラメータをご紹介します。
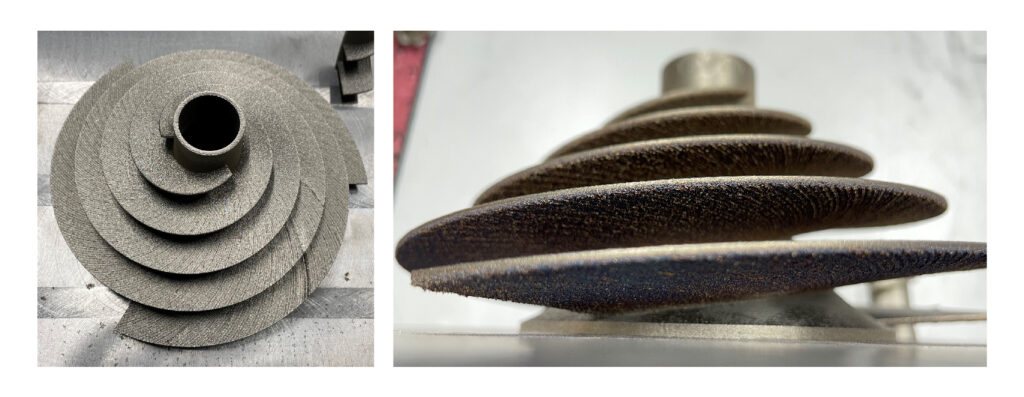
このスパイラル形状のオーバーハングは5度で、使用した材料はオーバーヒーティングしやすいMS1(マルエージング鋼)です。
通常だと、オーバーヒーティングによる変形が発生し、パーツがリコーターブレードに干渉して造形がストップしやすい形状です。
このパーツはSmart Fusionを使用せずに造形しました。
EOSのSmart Fusionは、単なる製造のツールとしてだけでなく、造形の可能性を広げるような新しいパラメータ開発のための学習ツールにもなります。
結晶を特定の方向に成長させるパラメータ
EOSのパートナー企業のAdditive Flow社の事例です。
負荷が最も高くなる部分の微細組織をテーラーメイドしました。
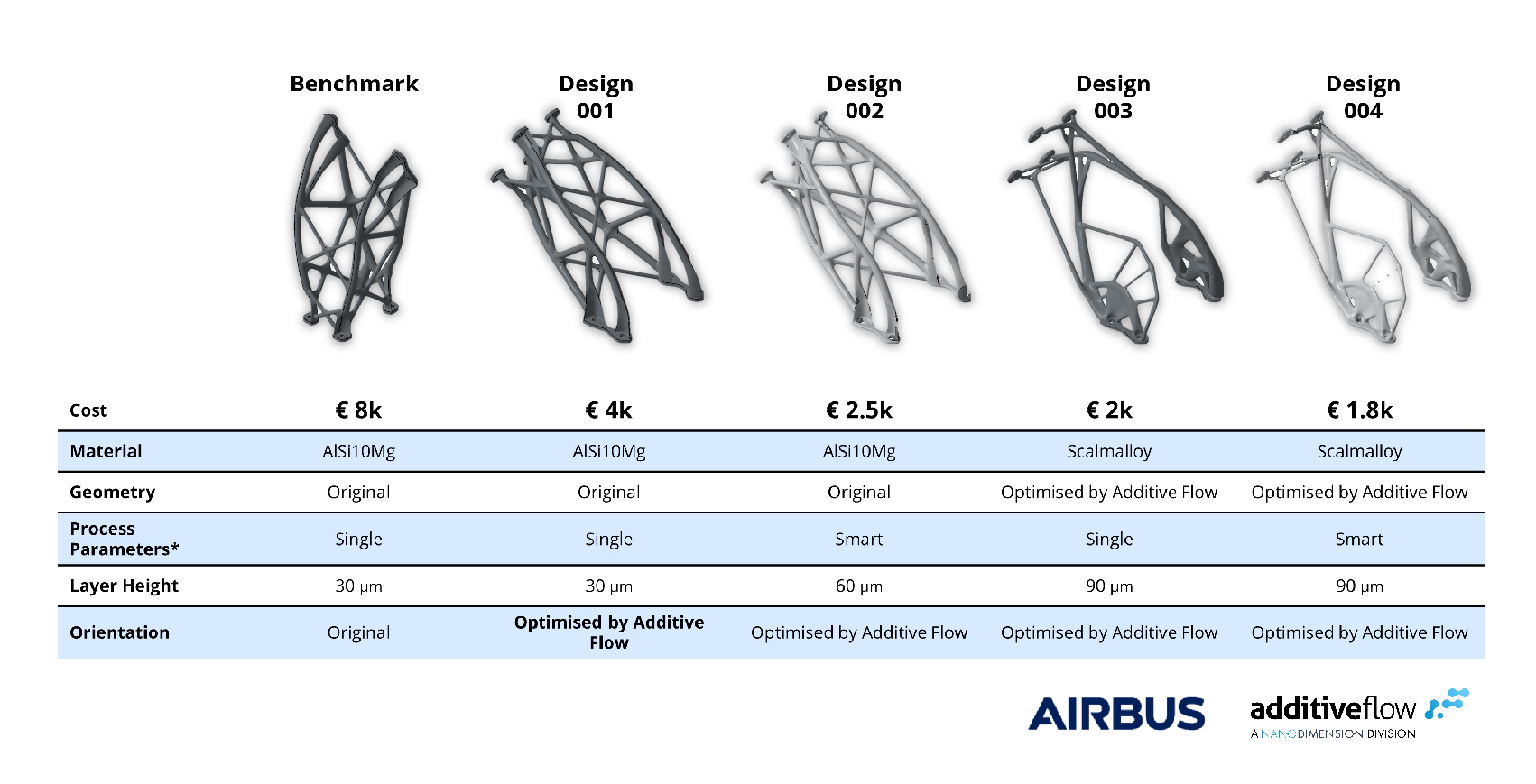
一般的には等方性の高い特性を希望するお客様が多いですが、今回は極めて異方性の高い特性を利用しました。
ここでご紹介したイノベーションを、全てまとめて「スマートプロセス」と呼んでいます。
スマートプロセスを活用することで、アプリケーション開発に多くのアドバンテージをもたらすでしょう。
部品単価を下げる方法
3Dプリンターで製造した部品の単価を下げるためには、マシンをできる限り稼働させ、造形エリアを最大限に活用して一度に多くのパーツを造形することが大切です。
多くの人が、レーザーの本数を増やせば増やすほど、生産性が向上しコストが下がると思っているはずです。
しかし、実際はそうとも言えません。
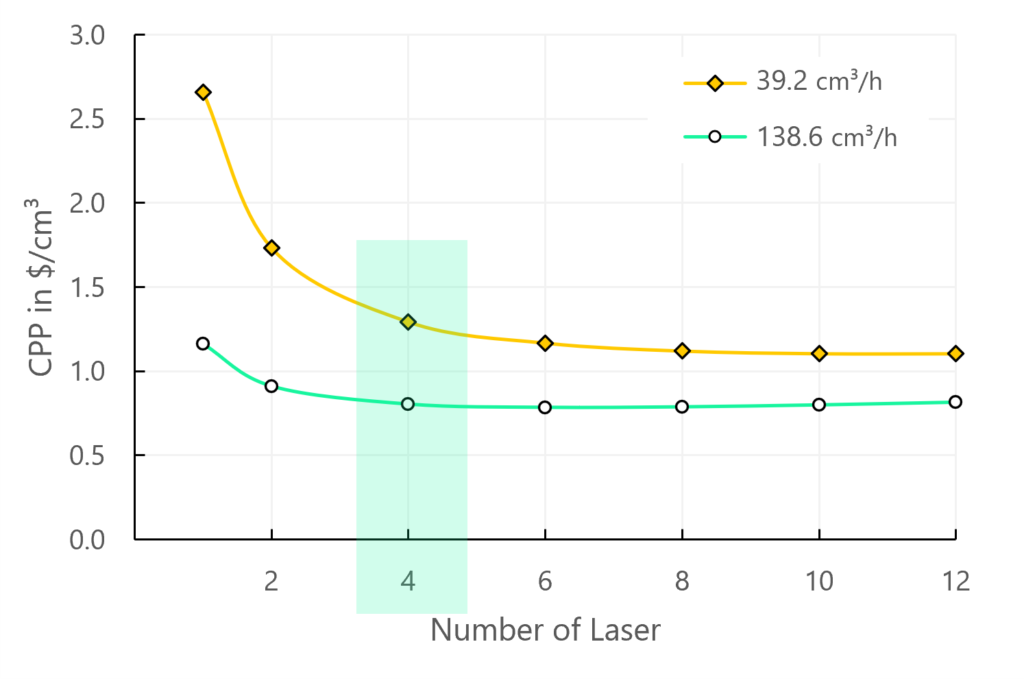
光学系は3Dプリンターを構成する部品の中でも最も高価な部品です。
レーザーの本数を増やすにつれて、マシン本体の価格も上がり、結果的に部品単価にも影響を与えます。
最後に
EOSのグループ会社であるAMCMは、皆様のアプリケーションに合わせた3Dプリンターのカスタマイズをご提供いたします。
それぞれの用途に特化した構成の3Dプリンターを使うことが、アディティブ・マニュファクチャリングの適用を成功させるでしょう。