ドイツのEOS本社では日々さまざまな技術開発を行っています。
今回はEOS社 イノベーション部代表のMichael Jan Galba氏に3つのテーマに沿った研究について説明していただきました。
※本記事は、2023年2月2日に開催された、TCT Japan 2023 Introducing Stageでの講演をもとに構成しています。
目次
- 微細な造形を可能にする技術 パルスレーザー モジュレーションとFine Detail Resolution
- 生産性向上によりコスト削減を狙う技術 Big SpotとBeam Shaping
- サポートフリーを実現する技術 Smart Fusion
それぞれについて、事例とともにご紹介いたします。
パルスレーザー モジュレーション
パルスレーザーモジュレーションは通常とは全く異なる方法でレーザー照射を行う技術であり、非常に微細な造形を行うことができます。
そのため、微細な設計がされている形状部分はパルスレーザーで照射し
その他のバルク/肉厚形状においては通常の照射で行うといった具合に、レーザー照射の種類を組み合わせることで非常に効果的な造形ができます。
あくまでソフトウェアで実現する技術ですので、EOS PRINT(ソフトウェア)のバージョン2.8以上であればパルスレーザーの変調操作が可能で、
EOS M290を始めとして、EOS M400シリーズ、EOS M300シリーズの金属3Dプリンターで利用が可能です。
パルスレーザー変調 EOS IN718(インコネル)での試験
インコネルは耐熱性と耐食性に優れている材料です。
パルスレーザーの変調を行い、板厚およそ120μmと90μmのサンプルを造形し、その後2気圧の水密性能試験を行いました。
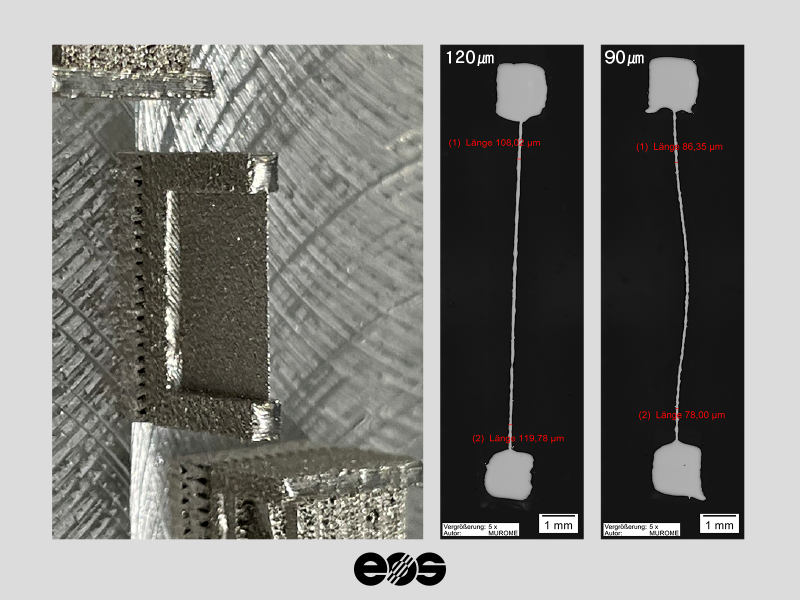
板厚90μmの水密性試験は失敗となりましたが、もし水密性が必要なければ、造形そのものとしてはもう少し厚みを薄くすることも可能です。
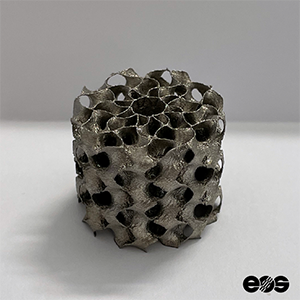
こちらは先ほどのパルスレーザー変調技術を利用して造形した、板厚120μmのジャイロイド構造です。
(参考:ジャイロイド構造とは)
とても軽いのでアルミニウムかと勘違いしてしまいますが、インコネルで造形されています。
熱交換器にわざわざインコネルを選ぶ人はあまりいないと思いますが、
板厚を十分に薄くすることができれば、素材の伝導性はあまり問題にならなくなります。
用途に応じた板厚を実現させることで、部品の性能を大幅に向上させることができます。
パルスレーザー変調 EOS AlSi10Mg(アルミニウム)での試験
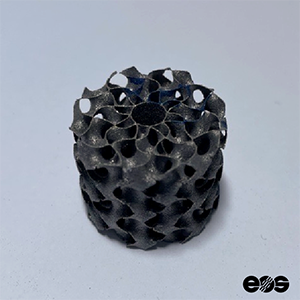
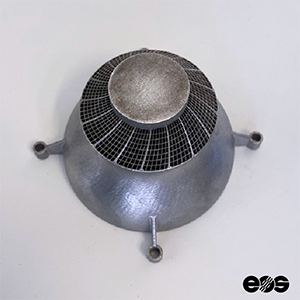
お客様から「アルミニウムで造形できますか?」というご質問をよくいただきます。
AM造形では粉末の熱的性質が品質にも影響を与えるので、アルミニウムはインコネルほどの水密構造が難しい材質ではあります。
そのため、今回は水密・気密性を持たせるため、インコネルよりも厚めのおよそ150μmの板厚で造形し、試験を行いました。
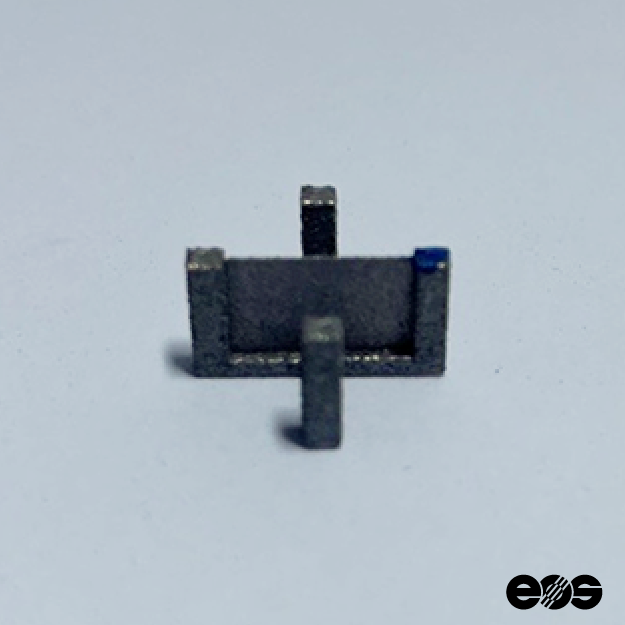

試験は上記の写真の通り、水中でのエアーによる気密テストを行いました。
もし水中で気泡が見えてしまうと水密構造ではないということですので、パラメータ最適化のプロセスまで工程を戻す必要がありますが、
今回のインコネル及びアルミニウムでの試験は成功に終わりました。
このような難しい薄板の造形も、EOSの金属3Dプリンターではソフトウェアでパルスレーザーの変調を行うだけで実現できる技術になっております。
パルスレーザー変調 造形例 /EOS MS1
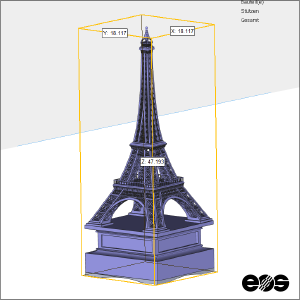
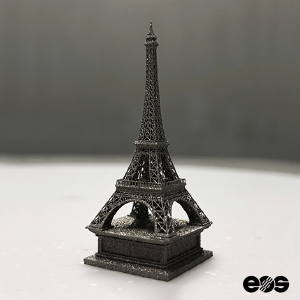
土台は約18mm角、高さは約47mmというとても小さい造形物で、材質はEOS MS1(マルエージング鋼)です。
細かい支柱やダウンスキン部分への粉末の付着、土台の面粗度など、造形上難しい箇所が沢山ある形状ですが、
緻密さが必要とされる部分にのみパルスレーザーの変調パラメータを適用することで、品質を大幅に改善することができます。
以下にパルスレーザーの変調が適用されたもの(ON)と、適用されていない従来のもの(OFF)とを比較しています。
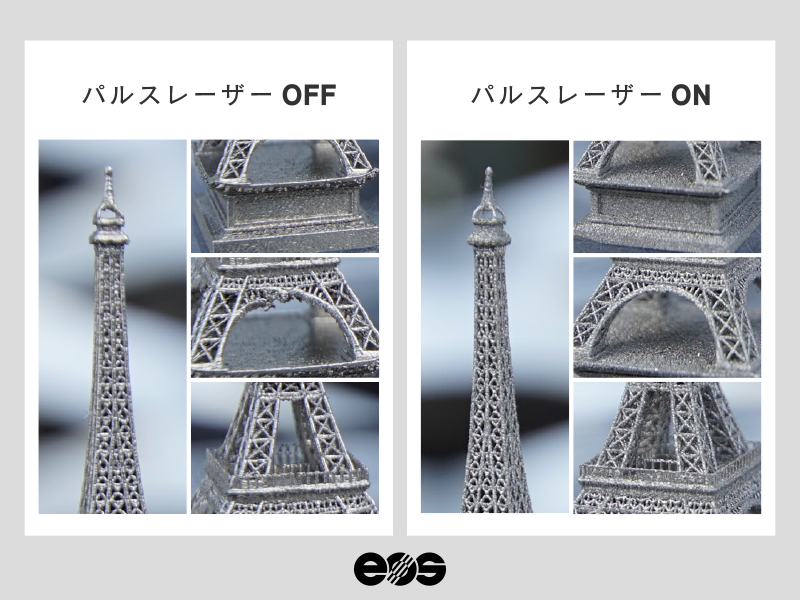
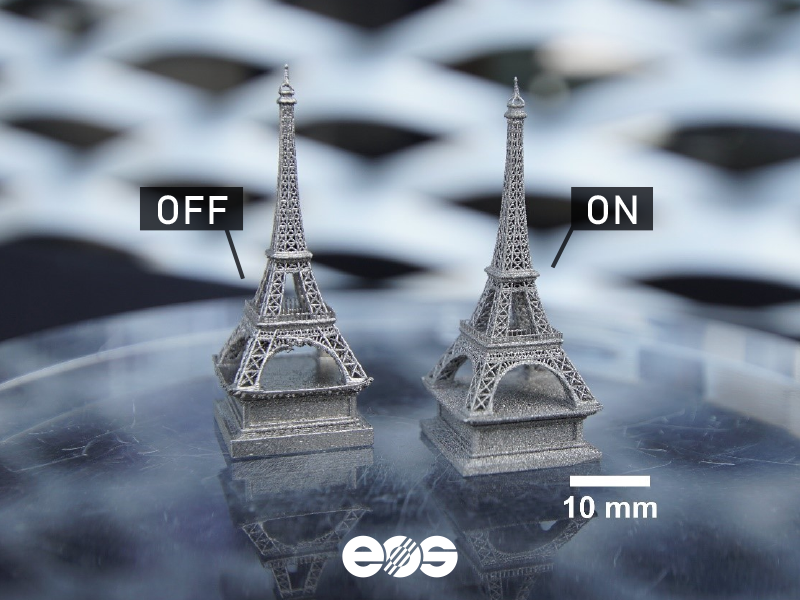
パルスレーザーの方が梁のシャープさや鮮明さが際立っているだけでなく、通常だと造形できない水平になっている箇所も全く問題なく造形できています。
AM造形の場合、直径にもよりますが円弧状の構造はダウンスキンとなり、表面粗度が悪くなる傾向がありますが、
この事例のようにパルスレーザーの変調だけで表面品質は改善できるのです。
FDR (Fine Detail Resolution)
FDR技術は、3Dプリンターの光学系を改造し照射のフォーカス径を非常に小さくすることで、細部の解像度を高める技術です。
EOS標準機のフォーカス系が80μmのところ、FDRでは半分の40μmが可能です。
FDR 造形例/ EOS 17-4PH
FDR技術を活用して非常に微細な造形を行った例をご紹介します。
材質は17-4PH(ステンレス鋼)で、チェーンの連結部分は80μmという細かさで造形されています。
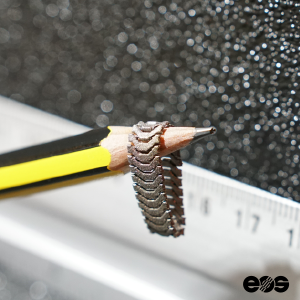

今回は80μmの可動部の精度を上げるため、通常よりも細かい粉末材料を利用しています。
細かい粉末は均一に敷き詰めること(=リコーティング)が難しくなるため、ここではリコーティング技術とフォーカス系に変更を加えました。
このように非常に高度なアプリケーションの開発となると、最終的にハードウェアのカスタムに辿り着く場合があります。
基本的な光学系の改良で済むのか、根本的なマシンの改良なのかは、お客様の求めるものによります。
EOS装置のハードウエアの改良は、私が所属するEOSイノベーションプロジェクトや、
EOSの100%関連会社であり装置のカスタム専門事業を行うAMCM社が責任をもって担当するので、ご安心ください。
Big Spot
Big Spotは、レーザー照射のスポット径を変更することができる、EOSが開発中の技術です。
この技術は新しいスキャナーを基盤としており、フォーカスを非常に素早く合わせることができます。
また、最大3kWまで出力を増大させることも可能です。
こちらは造形プロセスの比較映像です。
左側は標準のプロセスで、右側はBig Spotを利用した1kWでの照射プロセスです。
生産性が全く違うことが分かると思いますが、両方ともレーザーの本数は一本で、品質結果も同じです。
Big Spot 造形事例
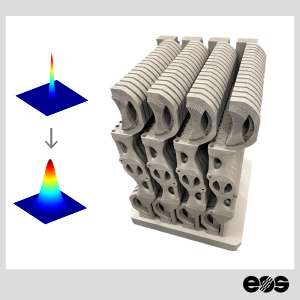
材料:AlSi10Mg
使用装置:M300-4 *1kWレーザーを4本搭載
造形時間:30時間
従来比で造形時間を70%削減(108時間⇒30時間)
プロセス/レーザー速度は40-50㎣/s
ドイツで開催されたFormnext2021でも注目を浴びた、アルミ製のツールチェンジャーです。
Big Spotの活用によって、パーツの特性は要求値を充足させたまま造形時間が70%も短縮しました。
前出のAMCM社がこのような装置のカスタムを担当しています。
EOSのベストセラー機であるM290をベースとして、異なるレーザーを搭載したりシステムを改造したりして、
M290にビーム形状のプログラミングが可能なレーザーを2本搭載した装置などを開発しています。
※M290は本来レーザーが1本の機種です。
Beam Shaping
Beam Shapingとは、レーザー照射を任意のビーム形状に切り替えられる、EOSの独自の技術です。
ミリ秒単位の素早さでビーム形状の切り替えを行うことができます。
標準的なレーザー照射はガウシアンビームと呼ばれる形状ですが、
この技術を利用するとドーナツ型やフラットトップ型、アシンメトリー型など様々な形状でのレーザー照射が可能です。
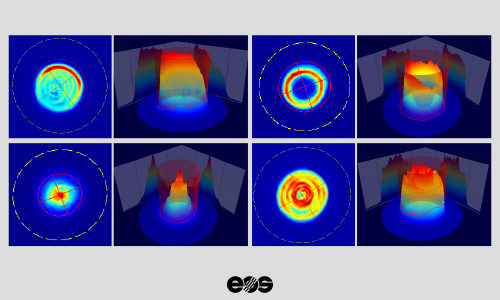
ビーム形状を変更することで入熱も変わるため、
短時間でより多くのエネルギーを吸収する方法を材料種ごとに研究し、入熱条件を最適化しています。
こちらはBeam Shapingを利用したプロセスの様子です。
ヒュームやスパッタなど溶融池(メルトプール)の様子がよく観察でき、それぞれはっきりと挙動の違いを確認できると思います。
この技術をアプリケーションに適用した例をご紹介します。
この2つは全く同じレーザー出力で、ビーム形状だけが異なります。
左側は標準のガウシアンビーム、右側はBeam Shapingを利用しています。
右側のBeam Shapingでは、塗りつぶし部分をフラットトップビームで広範囲を一気に照射し、
輪郭線には輪郭用の細いビームを、そして最後の何本も線を引く部分では1つのビームを3つに分割し、一気に照射させています。
そのため、全く同じ出力・レーザー本数でも、右側の方が2.5倍速く造形ができています。
Beam Shaping 造形事例
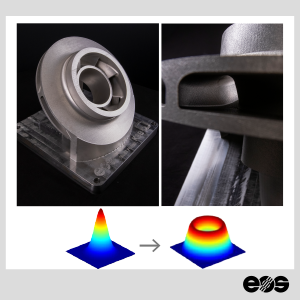
材料:IN625(インコネル)
使用装置:AMCM M4K-4 *1.2kWレーザーを4本搭載
造形時間:32時間(積層厚80μm)
└ 従来比で造形時間を76%削減(135時間,40μm⇒32時間,80μm)
サポート除去時間は95%削減
内部のサポート構造も96%削減
AMCM社によるカスタム機、M4K-4で直径400mmのクローズドインペラーを造形しました。
EOS標準機のシミュレーション上の造形時間では135時間でしたが、カスタム機で造形すると32時間で完成しました。
造形時間の短縮だけでなく、欠陥のない微細構造の造形が可能になります。
Smart Fusion
Smart Fusionは、造形ができない形状を造形可能にしてしまう技術で、AM技術における最大のゲームチェンジャーだと言えます。
この技術の活用によって、サポートフリーでの造形も可能になります。
Smart Fusionでは、造形中の熱画像を感知しています。
そのため、もしある箇所でオーバーヒート(加熱)が発生していたら、3Dプリンターが自動的に次の積層でプロセスを調整します。
金属AMで必要となる『サポート構造』と呼ばれる足場は、レーザーによる熱を逃がすために必要なのですが、
Smart Fusionによる「装置のプロセス自動調整」によって熱だまりを無くすことができ、結果的にサポートフリーで造形ができるのです。
サポート構造の造形がないことで造形時間が短縮され、サポート除去に必要だった時間も無くなり、リードタイムが大幅に削減できました。
また、人の手によるサポート除去がなくなり、使用する材料粉末の量も削減しているため、コストも大幅に削減できています。
Smart Fusion 造形事例
パートナー企業であるロンチャースペース社のロケットエンジン用推進剤タンクの造形事例をご紹介します。
人工衛星のデータ伝送装置用のプロペラタンクで、実際に飛ぶものに利用されています。
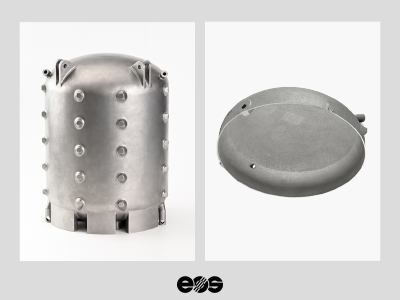
右側は上部をカットしたもので、ドーム面にサポートがないことが分かる。
使用装置:M300-4 *400Wレーザーを4本搭載
ドーム内部もサポートフリーで造形
サポートフリーにより造形時間が80%削減。
このタンクは直径300mm、高さ400mmで、内部が中空構造となっています。
金属AMについて少しでも知っている人であれば、これをサポートフリーで造形できる訳ない!と思うはずですが、
Smart Fusionのおかげでドーム形状の内部にサポートが一切ついていません。
Smart Fusion 造形事例
次にチタン製のロードバイクのペダルをご紹介します。
とても負荷がかかるパーツでもあり難しいケースでしたが、サポート構造を利用してパーツを積み重ね、Smart Fusionで効率的に造形ができました。
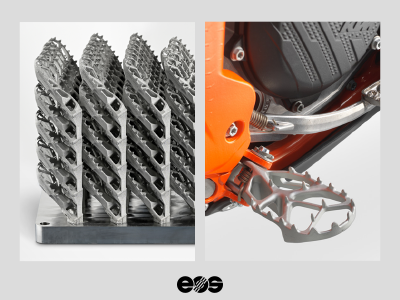
一度に造形できる個数が多いと、パーツ単価が下がる。
材料:Ti64 (チタン)
使用装置:M400-4 *400Wレーザーを4本搭載
サポート構造 50%削減
造形時間 36%削減(1パーツあたり)
コスト 26%削減
ポストプロセスの時間 60%削減
もちろん疲労寿命の要件にも合格しています。
ペダルを積み上げている繋ぎ目部分は手で簡単に取ることができ、後処理がほとんど不要となりました。
最後にKSB社の大きなインペラーをご紹介します。
こちらは海水ポンプとして非常に過酷な環境下で利用されており、重さはおよそ35kgという大きなパーツです。

材料:IN 625 (インコネル)
使用装置:M400-4 *400Wレーザーを4本搭載
造形時間 61時間
└ 従来比で造形時間を55%削減(135時間⇒61時間)
内部のサポート構造 96%削減
サポート除去の時間 95%削減
このようなクローズドインペラーは形状的に内部にサポート構造が必要となりますが、サポートの除去が非常に大変な作業となります。
Smart Fusionを適用することで内部のサポート構造を無くし、結果的に造形時間を半減し、後処理工程も削減、それによるコスト削減を実現できました。
Smart Fusionの品質への影響について
お客様からは、「装置が自動でオーバーヒート部分のプロセス調整を行うなんて、品質に影響はないのか」とご質問をいただきます。
こちらは最初の造形物です。
プロセスの最適化が非常に難しいアプリケーションでしたため、初回は全体の75%しか造形ができませんでした。
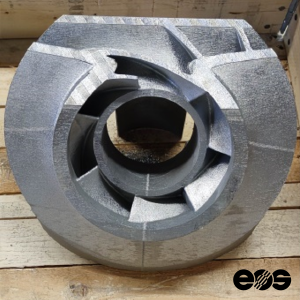
この造形物を利用して、実際に装置による自動プロセス調整が発生した箇所でカットし、内部欠陥を分析しました。
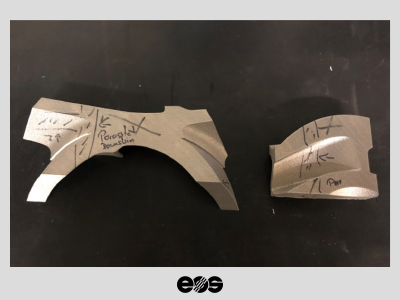
断面観察を行った結果が以下となります。
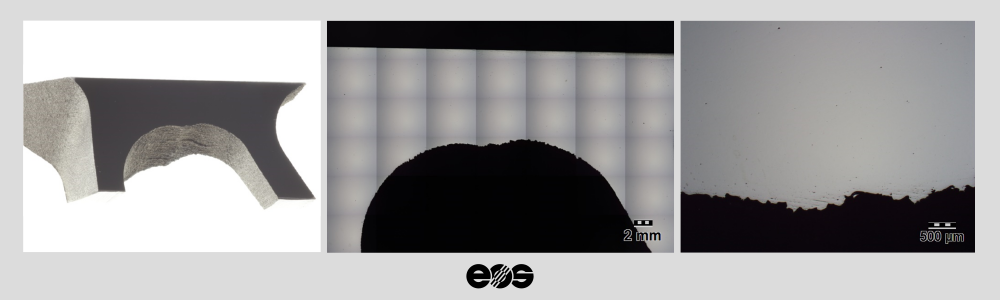
造形が難しい箇所でもこのようにしっかり造形できており、プロセスの異常はありません。
写真をご覧の通り、完璧な微細構造と密度であることが確認できます。
つまり、装置によるプロセス調整で品質に影響を及ぼすことはありません。
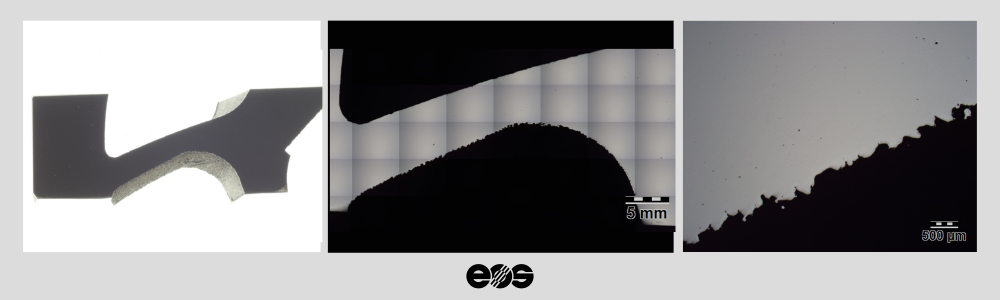
拡大した時に見えるこれらの気孔は標準の範囲内で発生するものですので、むしろ私たちの想定通りに出ています。
ここまで、緻密な構造とサポートフリー、生産性向上の技術についてご紹介させていただきました。
最後になりますが、我々は皆さまと一緒に課題を解決したいと思っていますので
ぜひアプリケーションと抱えている問題を我々に教えてください。
AMCM社はEOSの100%関連会社で、EOSの3Dプリンターをお客様のご要望に応じて造形領域やレーザーの種類・出力などをカスタムする専門の会社です。
日本のお客様にも弊社からご提供可能な装置となっております。
今回ご紹介した技術を実際に使っての技術検証も可能でございます。
詳細のご説明やお打合せについては、弊社までお気軽にお問い合わせ頂けますと幸いです。
最後までご拝読いただきありがとうございました。
(株)NTTデータ ザムテクノロジーズでは、
3Dプリンター、用途開発、受託製造、金属材料開発など、3Dプリンティングに関する質問やお問合せを受け付けております。