
前報①で、SLM用Ni基超合金ALLOY 718(ニッケル基超合金、IN718相当)のガスアトマイズ粉末とプラズマアトマイズ粉末の違いについて
紹介しましたが、本報では実際に金属3Dプリンター(EOS M 290)で造形した時の違いについて紹介します。以下、造形条件は統一しています。
図1に造形体のアルキメデス密度、図2にHRB硬さ(ロックウェル硬さ)を示します。

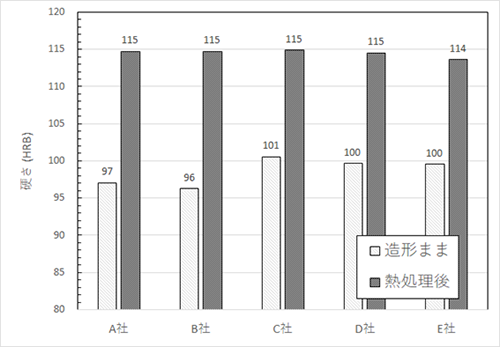
アルキメデス密度は、全面を軽く研磨し表面の凹凸を除いてから測定を実施しました。 各社いずれも約8.2g/㎤あり、明確な違いはみられませんでした。 HRB硬さは、造形方向に沿って切断した面を研磨後に測定しました。造形ままではいずれも約100HRB、熱処理後ではいずれも約115HRBであり、アルキメデス密度同様に明確な違いはみられませんでした。
図3にダウンスキン及びアップスキンの平均粗さSa、表1にレーザー回析・散乱式 で測定した原料粉末の粒度を示します。
参考:表面粗度改善 ―ダウンスキンとは?―【EOS 金属3Dプリンター】
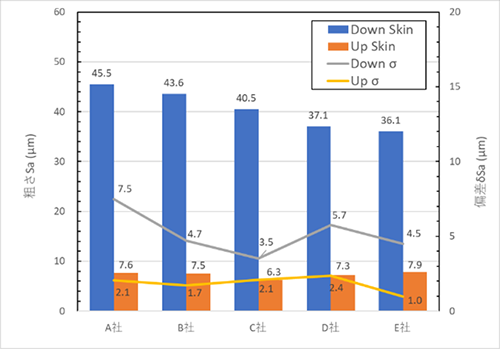
D10(㎛) | D50(㎛) | D90(㎛) | SD(㎛) | +45㎛含有率 | -10㎛含有率 | |
---|---|---|---|---|---|---|
A社 | 15.4 | 30.0 | 52.1 | 13.6 | 16.6 | 1.9 |
B社 | 18.0 | 32.1 | 54.2 | 13.5 | 19.7 | 0.7 |
C社 | 24.4 | 33.7 | 49.4 | 9.3 | 15.6 | 0 |
D社 | 23.1 | 34.8 | 52.2 | 10.9 | 19.9 | 0 |
E社 | 28.9 | 38.3 | 52.6 | 8.9 | 24.2 | 0 |
各社アップスキンの粗さは6~8μmであり大きな違いはみられませんでしたが、ダウンスキンの粗さではA、B社は43~46μm、C社は40.5μm、 D、E社は36~37μmと明確な違いが確認できました。 ここで興味深いのは、ダウンスキンの粗さ(Sa)は、粉末の粒度の大きさ(+45μm粉末含有率)よりも、標準偏差(SD)と相関があるかもしれないという事です。ここでSDと表現しているのは統計学上の標準偏差ではなく、粒度の分布幅の目安となるものです。
ダウンスキンの粗さSaの値が大きかったA~C社は、値の小さいD、E社と比較すると粒度の大きい粉末(+45μm粉末)の割合が少ない半面、粒度分布幅の目安であるSDの値が大きく、粒径が揃っていないことが分かります。ここから、ダウンスキンの粗さSaはSDと相関があると推測しています。しかし、C社で必ずしもそのような相関がみられていないのは、前報①に報告した粉末時の状態が起因していると推測しています。つまり、SDが小さくても流動性が悪い粉末では、C社のようにダウンスキンの粗さSaが大きくなる可能性があるということです。
これらの結果から、造形後の面粗度の改善を目指す方法として粉末の選定も考える必要のある要素であり、粒径が揃った粉末かつ流動性が優れた粉末を使用することが重要だと考えています。